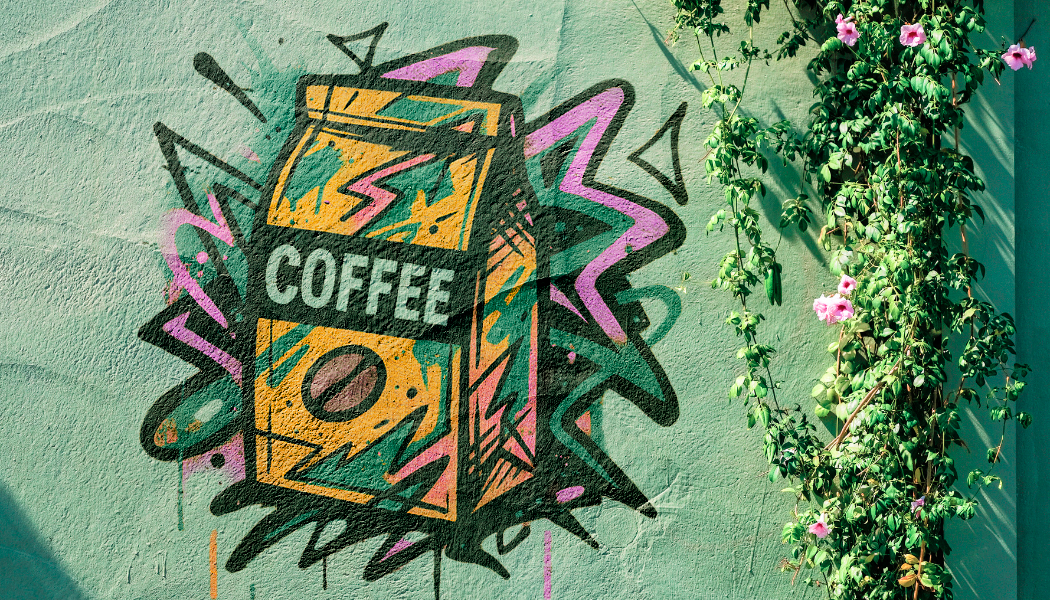
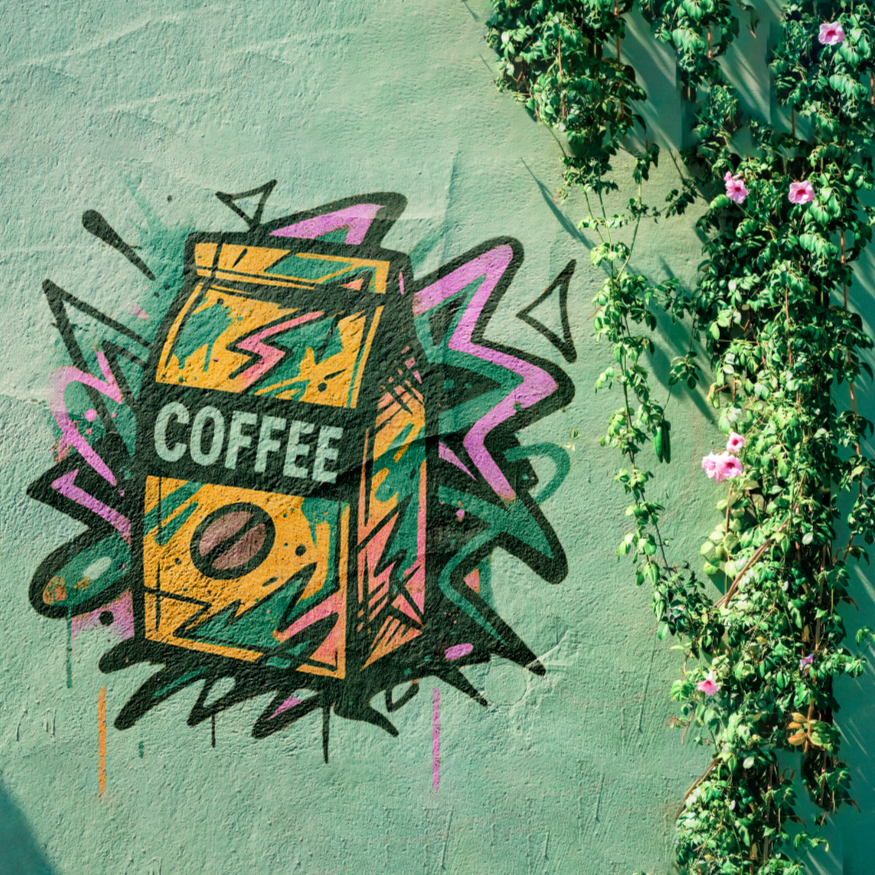
Yes, our products are PFAS-free. PCKG, as a responsible packaging manufacturer, is committed to eliminating the use of perfluoroalkyl and poly-fluoroalkyl substances (PFAS) in our packaging materials. As of January 1st, 2023, all our products are PFAS-free. We recognize the
environmental and health concerns associated with PFAS and have taken proactive measures to phase out their use. By doing so, we prioritize the well-being of our customers and the ecosystems in which our products are used.
While we understand the growing demand for compostable materials, our decision not to offer
them is rooted in our dedication to sustainability and a comprehensive understanding of the packaging industry. Compostable materials require specific conditions, such as industrial composting facilities, to break down efficiently. Without these facilities, compostable materials
may end up in landfills, where they can contribute to methane emissions and fail to degrade as intended. They also require constant refrigeration during transport and storage for the intended use; therefore, more fossil fuels are used, and the pros of compostability no longer apply. We
believe in promoting solutions that are accessible, practical, and aligned with the existing waste management infrastructure. Therefore, we focus on recyclability, collectability, and the efficient utilization of materials, striving to minimize waste and reduce our environmental impact through these approaches.
PP and PE are both types of plastic materials commonly used in packaging. Here's a brief explanation of the differences between the two: Polypropylene (PP): PP is a versatile thermoplastic polymer known for its durability and resistance to high temperatures. It is commonly used in packaging products such as food containers, caps, and closures. PP offers excellent chemical resistance, making it suitable for storing various substances. It is also known for its relatively low environmental impact, as it can be recycled.
Polyethylene (PE): PE is another widely used thermoplastic polymer that comes in various forms, including high-density polyethylene (HDPE) and low-density polyethylene (LDPE). HDPE is known for its strength and rigidity, making it suitable for applications such as bottles, bags, and packaging films. LDPE, on the other hand, offers more flexibility and is often used for squeeze bottles, flexible packaging, and plastic wraps. PE is known for its recyclability, and some forms can be recycled multiple times.
While PP and PE have unique properties and applications, they are both recyclable materials that can contribute to a more sustainable packaging industry. At PCKG, we consider the specific requirements of each product and work with our clients to determine the most suitable material based on their needs and sustainability goals.
Please note that the information provided above serves as a general overview, and specific properties of PP and PE materials may vary depending on the manufacturing process and intended applications.
#4 refers to the resin identification code used to classify plastic materials. In the case of recycling, #4 corresponds to low-density polyethylene (LDPE), a type of plastic commonly used in packaging films, bags, and other flexible applications. When a product is labeled as #4
recyclable, it means that it is made of LDPE plastic, which can be collected, processed, and recycled into new LDPE products. Recycling #4 plastics helps to conserve resources and reduce waste sent to landfills.
While both terms relate to the breakdown of materials, there is a distinction between biodegradable and compostable:
Biodegradable: Biodegradable materials have the ability to naturally break down over time through the action of microorganisms, such as bacteria or fungi, in the environment. However, "biodegradable" alone does not specify the timeframe or conditions required for complete degradation. Some biodegradable materials may still leave behind harmful residues during the decomposition process.
Compostable: Compostable materials, on the other hand, undergo a specific process known as composting, which involves controlled conditions of heat, moisture, and microbial activity. Composting facilitates the breakdown of organic materials into nutrient-rich compost, which can be used as a beneficial soil amendment. Compostable products must meet stringent standards to ensure their ability to break down into non-toxic components within a defined timeframe.
It's important to note that not all biodegradable materials are compostable, but all compostable materials are biodegradable under the appropriate conditions. When considering environmentally friendly packaging options, understanding the specific certifications and requirements for biodegradability and compostability is crucial.
The cost of recyclable products can vary depending on several factors, such as the type of material used, the manufacturing process, and the market demand for recyclable materials. While recyclable packaging solutions may have a slightly higher upfront cost than conventional non-recyclable alternatives, their long-term benefits and environmental advantages often outweigh the initial investment. Additionally, as demand for recyclable products continues to grow and economies of scale come into play, the overall cost of recyclable packaging is expected to become more competitive. Companies prioritizing sustainability and investing in recyclable packaging solutions often find that the benefits, including enhanced brand reputation and consumer loyalty, outweigh potential cost differences.
The shelf life of recyclable products is primarily determined by the specific material used and the product's intended application. Recyclable materials, such as plastics, metals, and glass, can retain their quality and functionality if stored and used properly for extended periods. However, it's essential to consider that the recyclability of a product is not directly linked to its shelf life.
Recyclable products can maintain their integrity and functionality for extended periods when properly stored. Following manufacturer guidelines regarding storage conditions and shelf life recommendations for specific products is important. Ensuring appropriate storage and usage maximizes the shelf life of recyclable products, contributing to their overall sustainability.
Recyclable #4 coffee bags (made from LDPE—low-density polyethylene) are currently one of the best available options for balancing product protection and environmental responsibility. These bags offer excellent barrier properties that help preserve coffee freshness, flavor, and shelf life, which is crucial for reducing food waste. At the same time, they are made from a single material type, making them compatible with many existing recycling streams—unlike multi-layer or compostable alternatives that often require specialized facilities. While no packaging is perfect, recyclable #4 bags are a practical, scalable solution that supports both product integrity and a more circular economy.
Tu cesta está actualmente vacía.